What is Vacuum Forming?
Vacuum forming is a simplified version of thermoforming wherein a sheet of plastic is heated to a pliable forming temperature, shaped over a mold by applying a vacuum, and trimmed to create a usable product. This method offers an economical alternative to injection molding, especially for producing large parts, implementing design revisions, manufacturing large quantities, and creating padded foam-filled or laminated parts.
TRUSTED BY LARGE AND SMALL ORGANIZATIONS WORLDWIDE
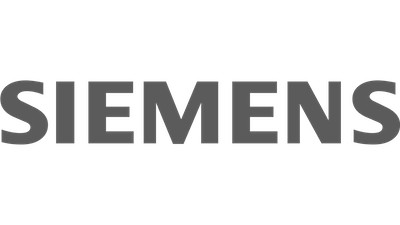

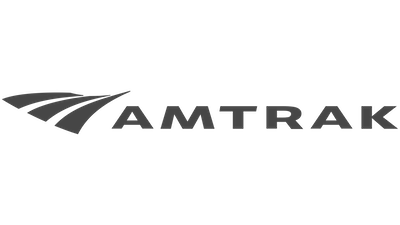
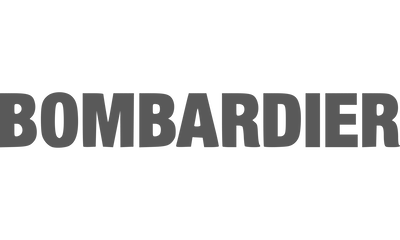


The Vacuum Forming Process
The vacuum forming process can be broken down into several key steps:
-
- Heating the Sheet: A plastic sheet is selected and heated until it becomes soft and pliable. This is the starting point of the process, making the sheet easy to manipulate and shape.
- Mold Placement: A male or female mold tool, depending on the required design, is mounted in a specialized machine.
- Applying the Heated Sheet: The heated plastic sheet is located over (or under, in some cases) the mold tool.
- Applying the Vacuum: A vacuum is applied to the space between the mold and the sheet, removing all air from the area. The vacuum pressure forces the heated sheet into contact with the mold surface, ensuring it conforms precisely to the shape of the mold.
- Cooling the Plastic: The atmospheric pressure holds the sheet against the mold until its temperature decreases below its heat distortion temperature. This ensures the plastic retains the shape of the mold as it cools and solidifies.
- Trimming: After the formed plastic has cooled and solidified, it is removed from the machine. The final product is then trimmed to the desired shape, removing any excess plastic.
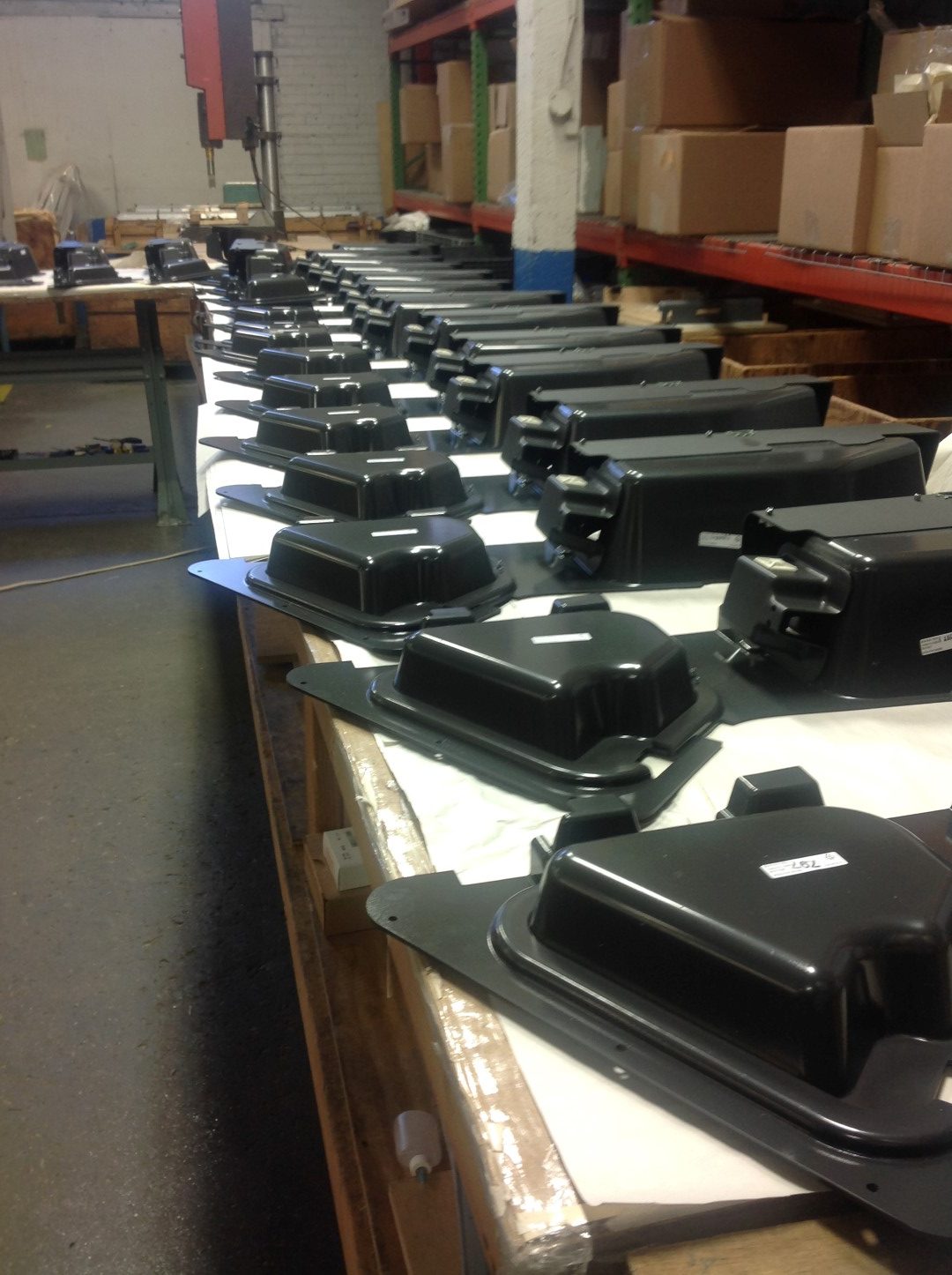
Benefits of Vacuum Forming
The vacuum forming process offers a range of advantages that make it a preferred choice over injection molding for certain applications:
- Cost-effectiveness: Vacuum forming is notably less expensive compared to other methods such as injection molding. This is especially the case when producing large parts, as the equipment and tooling costs are significantly lower.
- Design Flexibility: Vacuum forming allows for easy design revisions. If the design of a part needs to be changed, the mold can be easily adjusted or replaced without incurring high costs.
- Large Quantity Production: Vacuum forming excels in scenarios where large quantities of a product need to be produced. It enables efficient, repeatable production, making it an ideal method for mass production.
- Versatility: The process is suitable for creating padded foam-filled or laminated parts. The versatility of vacuum forming allows it to cater to a variety of industry needs, producing a wide range of products.
What do you need thermoformed?
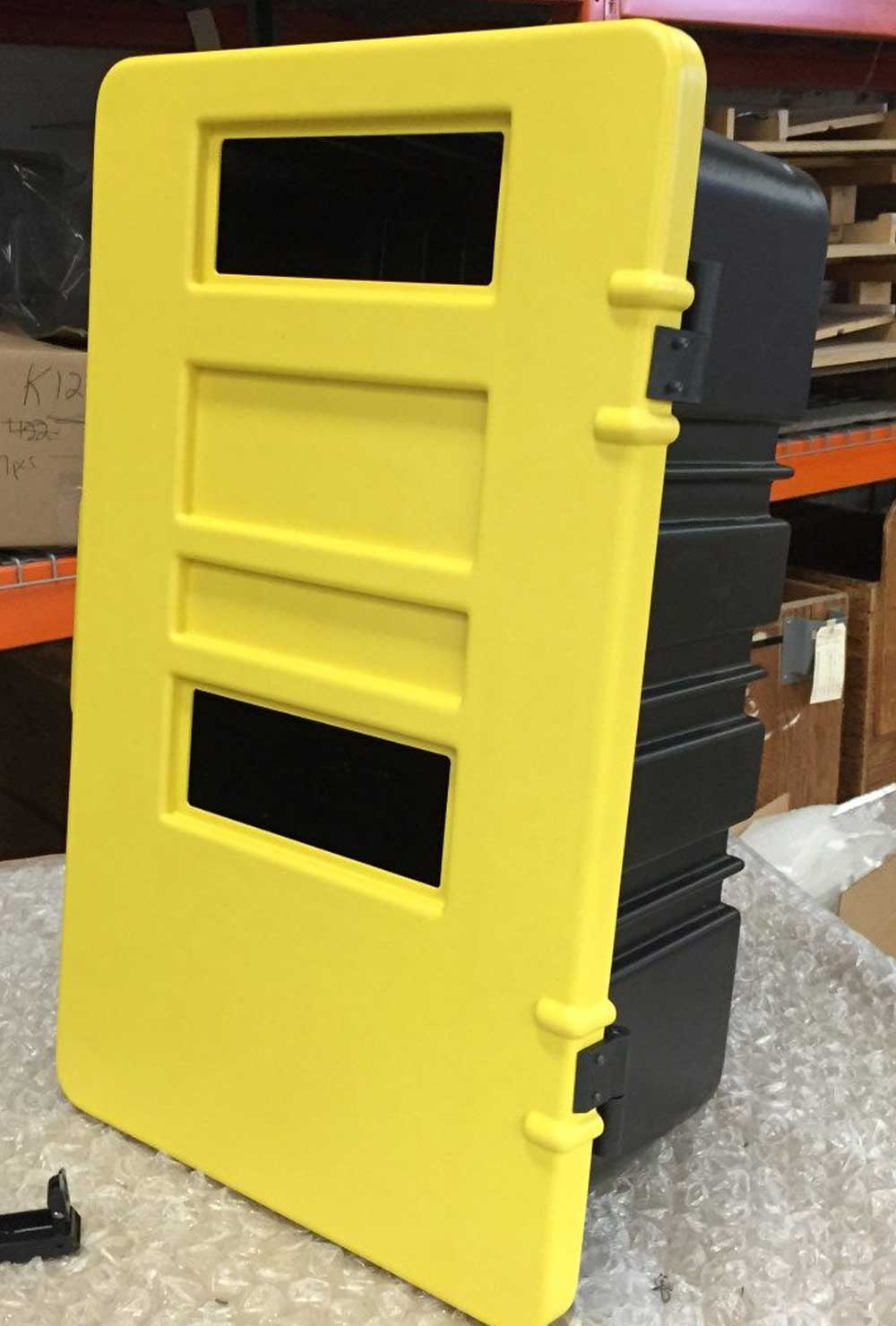
Applications of Vacuum Forming
Given its versatility and cost-effectiveness, vacuum forming is widely used in several industries including automotive, packaging, healthcare, and more. It’s ideal for creating packaging trays, vehicle door and dash panels, refrigerator liners, and other similar items.
Vacuum forming is an economical and flexible solution for the production of plastic parts, particularly large ones. Its efficient process, coupled with its low costs and versatility, makes it a widely adopted method in various industries.
For more information on vacuum forming or any other thermoforming process, don’t hesitate to contact us here at CWThomas.com. Our experienced team is always ready to provide guidance and help you with your specific needs.